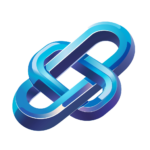
AI Driven Predictive Maintenance Workflow for Food Packaging Equipment
AI-driven predictive maintenance for food packaging equipment enhances efficiency by utilizing IoT sensors data analysis and automated scheduling for optimal performance
Category: AI Cooking Tools
Industry: Food Packaging Industry
Predictive Maintenance for Food Packaging Equipment
1. Data Collection
1.1 Sensor Integration
Install IoT sensors on food packaging equipment to monitor operational parameters such as temperature, humidity, vibration, and machine performance metrics.
1.2 Historical Data Compilation
Gather historical maintenance records and failure logs to understand past performance and identify patterns of equipment wear and tear.
2. Data Analysis
2.1 AI Model Development
Utilize machine learning algorithms to develop predictive models that analyze real-time data from sensors alongside historical data.
2.2 Tool Example: IBM Watson
Implement IBM Watson IoT to leverage its AI capabilities for data analysis and predictive insights, enhancing decision-making processes.
3. Predictive Analytics
3.1 Failure Prediction
Employ AI-driven analytics to predict potential equipment failures before they occur, allowing for timely maintenance interventions.
3.2 Tool Example: Siemens MindSphere
Utilize Siemens MindSphere for its advanced analytics capabilities to monitor equipment health and predict maintenance needs based on real-time data.
4. Maintenance Scheduling
4.1 Automated Alerts
Set up automated alerts for maintenance teams when predictive analytics indicate a high likelihood of equipment failure.
4.2 Tool Example: UpKeep
Use UpKeep’s mobile maintenance management software to streamline the scheduling and tracking of maintenance tasks based on AI predictions.
5. Implementation of Maintenance Actions
5.1 Proactive Maintenance
Conduct maintenance activities as indicated by predictive analytics to prevent equipment downtime.
5.2 Tool Example: Fiix Software
Leverage Fiix’s CMMS (Computerized Maintenance Management System) to manage work orders and track maintenance history efficiently.
6. Continuous Improvement
6.1 Performance Monitoring
Continuously monitor equipment performance post-maintenance to assess the effectiveness of predictive maintenance strategies.
6.2 Feedback Loop
Establish a feedback loop to refine AI models based on new data and maintenance outcomes, ensuring ongoing improvement in predictive accuracy.
7. Reporting and Documentation
7.1 Maintenance Reports
Generate comprehensive reports on maintenance activities, equipment performance, and predictive analytics outcomes for stakeholder review.
7.2 Tool Example: Tableau
Utilize Tableau for data visualization and reporting to present maintenance insights and trends to management effectively.
Keyword: Predictive maintenance food packaging equipment