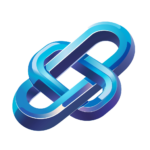
Proactive Equipment Failure Prevention with AI Integration
AI-driven workflow enhances equipment failure prevention through critical analysis monitoring predictive maintenance and continuous improvement for optimal performance
Category: AI Customer Service Tools
Industry: Manufacturing
Proactive Equipment Failure Prevention
1. Identify Critical Equipment
1.1 Inventory Assessment
Conduct a comprehensive inventory of all manufacturing equipment.
1.2 Criticality Analysis
Evaluate equipment based on operational importance and failure impact.
2. Implement AI-Driven Monitoring Tools
2.1 Sensor Installation
Equip critical machinery with IoT sensors to collect real-time data on performance metrics.
2.2 AI Analytics Platforms
Utilize AI-driven analytics tools, such as Siemens MindSphere or IBM Watson IoT, to process sensor data.
3. Predictive Maintenance Scheduling
3.1 Data Analysis
Leverage machine learning algorithms to analyze historical data and predict potential failures.
3.2 Maintenance Alerts
Set up automated alerts for maintenance teams based on predictive analytics insights.
4. Continuous Improvement Feedback Loop
4.1 Performance Review Meetings
Conduct regular meetings to review equipment performance and maintenance effectiveness.
4.2 Update AI Models
Refine AI models based on feedback and new data to enhance predictive accuracy.
5. Employee Training and Engagement
5.1 Training Programs
Implement training sessions on the use of AI tools and interpreting analytics for maintenance staff.
5.2 Employee Feedback Mechanism
Establish a channel for employees to provide feedback on equipment performance and AI tool usability.
6. Documentation and Reporting
6.1 Maintenance Logs
Maintain detailed logs of all maintenance activities and equipment performance metrics.
6.2 Reporting to Management
Generate regular reports for management outlining equipment health, maintenance actions, and AI tool effectiveness.
Keyword: Proactive equipment failure prevention