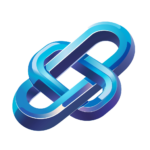
AI Powered Predictive Maintenance Optimization Workflow Guide
Discover an AI-driven predictive maintenance optimization workflow that enhances equipment performance through real-time data collection and advanced analytics
Category: AI Data Tools
Industry: Manufacturing
Predictive Maintenance Optimization Workflow
1. Data Collection
1.1 Sensor Data Acquisition
Utilize IoT sensors to gather real-time data on equipment performance, including temperature, vibration, and operational speed.
1.2 Historical Data Integration
Compile historical maintenance records and operational data from existing databases to provide context for predictive analysis.
2. Data Preprocessing
2.1 Data Cleaning
Implement data cleaning techniques to remove anomalies and ensure data accuracy.
2.2 Data Normalization
Normalize data to standardize measurements across different sensors and equipment types.
3. Feature Engineering
3.1 Identifying Key Features
Utilize domain expertise to identify critical features that influence equipment failure, such as usage patterns and environmental conditions.
3.2 Feature Selection
Employ AI-driven tools like Featuretools to automate the selection of relevant features for predictive modeling.
4. Predictive Modeling
4.1 Model Selection
Select appropriate machine learning algorithms such as Random Forest, Support Vector Machines, or Neural Networks for predictive analysis.
4.2 Model Training
Train the model using historical data and validated features, utilizing platforms like TensorFlow or PyTorch for deep learning approaches.
5. Model Evaluation
5.1 Performance Metrics
Evaluate the model’s performance using metrics such as accuracy, precision, recall, and F1 score.
5.2 Cross-Validation
Implement k-fold cross-validation to ensure model robustness and reduce overfitting.
6. Deployment
6.1 Integration with Manufacturing Systems
Integrate the predictive maintenance model with existing manufacturing systems using APIs or middleware solutions.
6.2 Real-Time Monitoring
Utilize AI-driven dashboards, such as those provided by Microsoft Power BI or Tableau, to visualize real-time data and predictive insights.
7. Maintenance Scheduling
7.1 Predictive Alerts
Set up automated alerts for maintenance teams based on predictive insights, utilizing tools like IBM Maximo or SAP PM.
7.2 Optimized Maintenance Planning
Leverage AI algorithms to create optimized maintenance schedules that minimize downtime and operational disruptions.
8. Continuous Improvement
8.1 Feedback Loop
Establish a feedback mechanism to continuously refine the predictive model based on new data and maintenance outcomes.
8.2 Performance Review
Conduct regular performance reviews to assess the effectiveness of the predictive maintenance strategy and make necessary adjustments.
Keyword: Predictive maintenance optimization