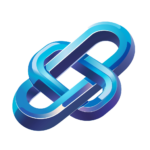
AI Driven Predictive Maintenance Workflow for Enhanced Efficiency
Discover an AI-driven predictive maintenance workflow that enhances equipment reliability through data collection analysis and real-time monitoring for optimal performance
Category: AI Design Tools
Industry: Manufacturing
Predictive Maintenance Workflow Using AI
1. Data Collection
1.1 Sensor Installation
Install IoT sensors on manufacturing equipment to collect real-time data on performance metrics such as temperature, vibration, and operating hours.
1.2 Data Aggregation
Utilize data aggregation tools such as Apache Kafka or AWS IoT Core to compile data from multiple sensors into a centralized database.
2. Data Preprocessing
2.1 Data Cleaning
Implement data cleaning processes using tools like Python’s Pandas library to remove inconsistencies and outliers from the collected data.
2.2 Data Normalization
Normalize data to ensure uniformity using techniques such as Min-Max scaling or Z-score normalization to prepare for analysis.
3. Predictive Analytics
3.1 Model Selection
Select appropriate AI models for predictive maintenance, such as regression analysis, decision trees, or neural networks. Tools like TensorFlow or PyTorch can be utilized for model development.
3.2 Training the Model
Train the selected model using historical data on equipment failures and maintenance records to identify patterns and predict potential issues.
3.3 Model Evaluation
Evaluate model performance using metrics such as accuracy, precision, and recall. Utilize tools like Scikit-learn for model validation and tuning.
4. Implementation
4.1 Integration with Manufacturing Systems
Integrate the predictive maintenance model with existing manufacturing execution systems (MES) using APIs or middleware solutions such as MuleSoft.
4.2 Real-Time Monitoring
Deploy the model for real-time monitoring of equipment health, utilizing dashboards created with tools like Tableau or Power BI to visualize data and predictions.
5. Maintenance Alerts and Actions
5.1 Alert Generation
Set up automated alerts to notify maintenance teams of predicted equipment failures through systems like Slack or Microsoft Teams.
5.2 Scheduled Maintenance
Plan and execute maintenance schedules based on predictive insights to minimize downtime and extend equipment lifespan.
6. Continuous Improvement
6.1 Feedback Loop
Establish a feedback loop to continuously refine the predictive model based on new data and maintenance outcomes, using tools like Jupyter Notebooks for iterative analysis.
6.2 Performance Review
Conduct regular performance reviews of the predictive maintenance workflow to assess its effectiveness and identify areas for enhancement.
Keyword: Predictive maintenance using AI