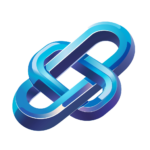
AI Driven Predictive Maintenance Workflow for Toy Manufacturing
AI-driven predictive maintenance in toy manufacturing enhances equipment reliability optimizes schedules and reduces downtime for improved operational efficiency
Category: AI Entertainment Tools
Industry: Toy and Game Manufacturing
Predictive Maintenance for Toy Manufacturing Equipment
1. Introduction to Predictive Maintenance
Predictive maintenance utilizes AI-driven tools to anticipate equipment failures and optimize maintenance schedules, thereby minimizing downtime and ensuring efficient production in toy manufacturing.
2. Data Collection
2.1 Sensor Installation
Equip manufacturing machinery with IoT sensors to collect real-time data on equipment performance, temperature, vibration, and other critical parameters.
2.2 Data Aggregation
Utilize cloud-based platforms to aggregate data from various sensors for comprehensive analysis. Tools such as AWS IoT or Microsoft Azure IoT can be employed for this purpose.
3. Data Analysis
3.1 AI Model Development
Develop machine learning models to analyze historical data and identify patterns that precede equipment failures. Tools like TensorFlow and PyTorch can be used to build these models.
3.2 Predictive Analytics
Implement predictive analytics algorithms to forecast potential failures. AI-driven platforms such as IBM Watson or Google Cloud AI can assist in this analysis.
4. Maintenance Scheduling
4.1 Automated Alerts
Set up automated alerts to notify maintenance teams when the AI model predicts a potential failure. This can be achieved using tools like Slack or Microsoft Teams integrated with monitoring systems.
4.2 Maintenance Planning
Utilize AI-driven scheduling tools to optimize maintenance workflows based on predictive insights, ensuring minimal disruption to production. Tools like UpKeep or Fiix can be effective in this regard.
5. Execution of Maintenance
5.1 Resource Allocation
Leverage AI tools to allocate resources effectively, ensuring that the right personnel and parts are available for maintenance tasks.
5.2 Performance Tracking
Monitor the performance of equipment post-maintenance using AI analytics to evaluate the effectiveness of the maintenance performed. Tools like Tableau or Power BI can visualize this data.
6. Continuous Improvement
6.1 Feedback Loop
Create a feedback loop where maintenance outcomes are analyzed to refine AI models and improve predictive accuracy over time.
6.2 Training and Development
Invest in training staff on AI tools and predictive maintenance strategies to foster a culture of continuous improvement within the organization.
7. Conclusion
Implementing a predictive maintenance workflow using AI in toy manufacturing not only enhances equipment reliability but also contributes to overall operational efficiency and cost savings.
Keyword: Predictive maintenance for toy manufacturing