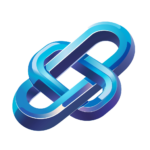
AI Driven Predictive Maintenance Workflow for Store Equipment
AI-driven predictive maintenance enhances grocery store operations by monitoring equipment health and scheduling proactive repairs to ensure efficiency and safety
Category: AI Food Tools
Industry: Grocery Stores
Predictive Maintenance for Store Equipment
1. Identify Equipment and Assets
1.1 Inventory of Store Equipment
Compile a comprehensive list of all equipment within the grocery store, including refrigeration units, ovens, scales, and checkout systems.
1.2 Prioritize Critical Equipment
Evaluate the impact of each equipment type on store operations, prioritizing those that are essential for maintaining food safety and customer service.
2. Data Collection
2.1 Sensor Installation
Install IoT sensors on critical equipment to monitor performance metrics such as temperature, humidity, and operational hours.
2.2 Data Aggregation
Utilize cloud-based platforms to aggregate data from various sensors for centralized analysis. Tools such as AWS IoT or Microsoft Azure can be employed.
3. Data Analysis
3.1 AI Model Development
Develop machine learning models to analyze collected data, identifying patterns and predicting potential equipment failures. Tools like TensorFlow or IBM Watson can be utilized for model creation.
3.2 Predictive Analytics
Implement predictive analytics to assess the likelihood of equipment failure based on historical data and real-time sensor inputs.
4. Maintenance Scheduling
4.1 Automated Alerts
Set up automated alerts to notify maintenance teams when predictive models indicate potential issues, allowing for proactive scheduling of repairs.
4.2 Maintenance Workflow Integration
Integrate findings into existing maintenance management systems (e.g., CMMS software like Hippo CMMS) to streamline scheduling and documentation.
5. Continuous Improvement
5.1 Feedback Loop
Establish a feedback loop where maintenance outcomes are analyzed to refine AI models and improve accuracy over time.
5.2 Training and Adaptation
Provide ongoing training for staff on new AI-driven tools and processes to ensure effective usage and adaptation to evolving technologies.
6. Reporting and Review
6.1 Performance Metrics
Regularly review performance metrics to assess the effectiveness of the predictive maintenance program, focusing on downtime reduction and cost savings.
6.2 Stakeholder Reporting
Prepare reports for stakeholders detailing the impact of predictive maintenance on operational efficiency and equipment longevity.
Keyword: predictive maintenance for grocery stores