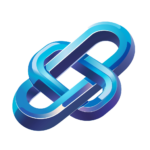
AI Driven Predictive Maintenance Workflow for Pipeline Networks
Discover how AI-driven predictive maintenance for pipeline networks enhances efficiency through real-time data collection model development and continuous improvement
Category: AI Networking Tools
Industry: Oil and Gas
Predictive Maintenance for Pipeline Networks Using Machine Learning
1. Data Collection
1.1 Sensor Data Acquisition
Utilize IoT sensors to gather real-time data on temperature, pressure, flow rates, and other critical parameters from pipeline networks.
1.2 Historical Data Integration
Aggregate historical maintenance records, incident reports, and environmental conditions to enrich the dataset for analysis.
2. Data Preprocessing
2.1 Data Cleaning
Remove duplicates, correct errors, and handle missing values in the collected dataset to ensure data quality.
2.2 Feature Engineering
Identify and create relevant features that may influence pipeline performance, such as time since last maintenance or environmental stressors.
3. Model Development
3.1 Selection of Machine Learning Algorithms
Choose appropriate algorithms for predictive maintenance, such as Random Forest, Support Vector Machines, or Neural Networks.
3.2 Training the Model
Utilize platforms like TensorFlow or PyTorch to train the selected machine learning models using the preprocessed data.
3.3 Model Validation
Employ techniques like cross-validation to assess the model’s accuracy and generalizability on unseen data.
4. Implementation of Predictive Analytics
4.1 Deployment of AI Models
Integrate the trained models into operational systems using cloud platforms such as AWS or Azure for scalability.
4.2 Real-time Monitoring
Utilize AI-driven monitoring tools like IBM Maximo or GE Digital’s Predix to provide real-time insights and alerts based on model predictions.
5. Maintenance Decision Support
5.1 Predictive Alerts Generation
Set up automated alerts for maintenance teams based on predictive analytics to facilitate timely interventions.
5.2 Maintenance Scheduling
Utilize AI tools to optimize maintenance schedules, minimizing downtime and operational disruptions.
6. Continuous Improvement
6.1 Feedback Loop Integration
Implement a system for continuous feedback from maintenance activities to refine and retrain models, ensuring ongoing accuracy and effectiveness.
6.2 Performance Metrics Analysis
Regularly analyze performance metrics such as prediction accuracy, maintenance costs, and downtime reduction to assess the impact of predictive maintenance initiatives.
Keyword: Predictive maintenance for pipelines