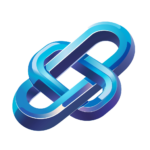
AI Driven Predictive Maintenance Optimization Workflow Guide
AI-driven predictive maintenance workflow enhances equipment reliability through real-time data collection analysis and continuous improvement strategies
Category: AI Productivity Tools
Industry: Manufacturing
Predictive Maintenance Optimization Workflow
1. Data Collection
1.1 Sensor Data Acquisition
Utilize IoT sensors to gather real-time data from machinery and equipment. Key parameters include temperature, vibration, and operational hours.
1.2 Historical Data Compilation
Aggregate historical maintenance records and machine performance data to identify patterns and trends.
2. Data Processing
2.1 Data Cleaning
Implement data cleaning techniques to remove anomalies and ensure data integrity using AI tools such as DataRobot or Trifacta.
2.2 Data Normalization
Normalize data to ensure consistency across different sources, facilitating accurate analysis.
3. Predictive Analytics
3.1 Model Development
Utilize machine learning algorithms to develop predictive models. Tools such as TensorFlow or Microsoft Azure Machine Learning can be employed.
3.2 Model Training and Validation
Train models using historical data and validate their accuracy through cross-validation techniques.
4. Implementation of Predictive Maintenance
4.1 Real-Time Monitoring
Deploy AI-driven dashboards using tools like Tableau or Power BI for real-time monitoring of equipment health.
4.2 Maintenance Scheduling
Utilize AI algorithms to predict optimal maintenance schedules, minimizing downtime and maximizing productivity.
5. Continuous Improvement
5.1 Feedback Loop
Establish a feedback mechanism to continuously improve predictive models based on new data and outcomes.
5.2 Performance Metrics Analysis
Regularly analyze key performance indicators (KPIs) to assess the effectiveness of the predictive maintenance strategy.
6. Reporting and Documentation
6.1 Generate Reports
Create comprehensive reports detailing maintenance activities, predictive insights, and overall equipment effectiveness (OEE).
6.2 Documentation of Processes
Document all processes and findings to ensure knowledge retention and facilitate future training.
Keyword: predictive maintenance optimization