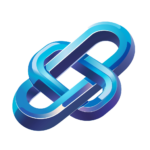
Automated Harvesting Robot Design with AI Integration Workflow
Discover an innovative automated harvesting robot designed to enhance efficiency reduce costs and improve crop yield through advanced AI integration and real-time decision making.
Category: AI Research Tools
Industry: Agriculture
Automated Harvesting Robot Design
1. Define Project Objectives
1.1 Identify Goals
Establish the primary objectives of the automated harvesting robot, such as increasing efficiency, reducing labor costs, and improving crop yield.
1.2 Stakeholder Engagement
Engage with stakeholders including farmers, agricultural experts, and technology developers to gather insights and expectations.
2. Research and Development
2.1 Market Analysis
Conduct a comprehensive analysis of existing automated harvesting solutions and identify gaps in the market.
2.2 AI Tools Exploration
Investigate AI research tools such as:
- TensorFlow: For developing machine learning models that improve robot navigation and crop recognition.
- OpenCV: For image processing tasks to identify ripe crops and avoid obstacles.
- ROS (Robot Operating System): For integrating various hardware components and software algorithms.
3. Design Phase
3.1 Conceptual Design
Develop initial design concepts for the harvesting robot, focusing on mobility, harvesting mechanisms, and AI integration.
3.2 Prototype Development
Create a prototype using 3D modeling software and simulation tools to visualize the design in action.
4. AI Implementation
4.1 Data Collection
Gather data from agricultural fields, including crop types, growth patterns, and environmental conditions.
4.2 Machine Learning Model Training
Utilize collected data to train machine learning models for:
- Crop identification and classification.
- Optimal harvesting times based on maturity levels.
4.3 Integration of AI Algorithms
Integrate AI algorithms into the robot’s control system to enhance decision-making capabilities in real-time.
5. Testing and Validation
5.1 Field Testing
Conduct field tests to evaluate the robot’s performance in real agricultural settings.
5.2 Performance Metrics Evaluation
Assess the robot’s efficiency, accuracy, and reliability based on predefined performance metrics.
6. Iteration and Improvement
6.1 Feedback Collection
Gather feedback from users and stakeholders to identify areas for improvement.
6.2 Design Refinement
Refine the robot’s design and AI algorithms based on feedback and performance data.
7. Deployment and Support
7.1 Production Scaling
Prepare for mass production of the automated harvesting robot, ensuring quality control and compliance with agricultural standards.
7.2 User Training and Support
Provide training for end-users on operating the robot and troubleshooting common issues.
7.3 Continuous Monitoring
Implement a system for continuous monitoring and updates to the AI algorithms to adapt to changing agricultural conditions.
Keyword: automated harvesting robot design