AI Training Tools to Bridge the Skills Gap in Manufacturing
Topic: AI Business Tools
Industry: Manufacturing
Discover how AI training tools can bridge the skills gap in manufacturing enhance workforce development and drive innovation for competitive advantage
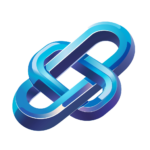
Navigating the Skills Gap: AI Training Tools for Manufacturing Workforce
Understanding the Skills Gap in Manufacturing
The manufacturing sector is currently facing a significant challenge: the skills gap. As technology evolves, the demand for a workforce adept in advanced manufacturing technologies, particularly artificial intelligence (AI), is increasing. This gap not only affects productivity but also hinders innovation and competitiveness. To address this issue, manufacturers must invest in training tools that leverage AI to equip their workforce with the necessary skills.
The Role of AI in Workforce Training
Artificial intelligence can play a transformative role in bridging the skills gap. By providing personalized learning experiences, AI-driven training tools can enhance the efficiency and effectiveness of workforce development programs. These tools can analyze individual learning patterns, adapt content accordingly, and provide real-time feedback, ensuring that employees gain the skills needed to thrive in a rapidly changing environment.
Key Benefits of AI Training Tools
- Personalized Learning: AI can tailor training programs to meet the specific needs of each employee, accommodating varying skill levels and learning speeds.
- Scalability: AI-powered platforms can easily scale training efforts across large organizations, ensuring consistent skill development.
- Data-Driven Insights: These tools can analyze performance data to identify skill gaps and recommend targeted training interventions.
- Engagement: Interactive and gamified training experiences can enhance employee engagement, making learning more enjoyable and effective.
AI-Driven Training Tools for Manufacturing
Several AI-driven tools are already making an impact in the manufacturing sector, providing innovative solutions to address the skills gap:
1. Siemens MindSphere
Siemens MindSphere is an open cloud-based IoT operating system that integrates AI and machine learning to optimize manufacturing processes. It offers training modules that help employees understand data analytics and machine performance, enabling them to make informed decisions on the shop floor.
2. PTC’s Vuforia
Vuforia is an augmented reality (AR) platform that utilizes AI to enhance training and maintenance processes. By providing real-time, hands-on training experiences, Vuforia allows employees to learn complex machinery operations in a safe and controlled environment, significantly reducing the learning curve.
3. IBM Watson
IBM Watson offers AI-driven solutions that can be utilized for workforce training in manufacturing. Its natural language processing capabilities enable the creation of intelligent virtual assistants that guide employees through training modules, answer questions, and provide instant feedback, ensuring a more interactive learning experience.
4. Udacity’s AI for Business Program
Udacity provides an AI for Business program that equips manufacturing professionals with essential AI skills. This online program includes hands-on projects and real-world case studies, allowing employees to apply their learning directly to their roles within the organization.
Implementing AI Training Tools Effectively
To successfully implement AI training tools, manufacturers should consider the following steps:
1. Assess Current Skills and Identify Gaps
Conduct a thorough assessment of the current skill levels within the workforce. Identify specific areas where training is needed to align with technological advancements and business goals.
2. Choose the Right AI Tools
Select AI training tools that best fit the organization’s needs. Consider factors such as scalability, ease of use, and the ability to integrate with existing systems.
3. Foster a Culture of Continuous Learning
Encourage a culture that values continuous learning and development. Promote the use of AI tools as integral to employee growth and organizational success.
4. Monitor and Evaluate Progress
Regularly monitor the effectiveness of training programs. Use data analytics provided by AI tools to evaluate employee progress and make necessary adjustments to training strategies.
Conclusion
As the manufacturing sector continues to evolve, addressing the skills gap through AI training tools is essential for maintaining competitiveness and driving innovation. By implementing these advanced technologies, manufacturers can empower their workforce, ensuring they are equipped with the skills needed to navigate the complexities of modern manufacturing.
Keyword: AI training tools for manufacturing