AI Upskilling for Factory Workers Essential Training for 2025
Topic: AI Career Tools
Industry: Manufacturing
Discover how AI is transforming factory worker training for 2025 with smart tools immersive experiences and continuous learning strategies to enhance skills and efficiency
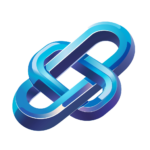
How AI is Upskilling the Modern Factory Worker: Essential Training for 2025
The Evolving Landscape of Manufacturing
The manufacturing industry is undergoing a profound transformation, driven by advancements in artificial intelligence (AI). As factories increasingly adopt smart technologies, the role of the factory worker is evolving. To remain competitive, organizations must focus on upskilling their workforce, equipping them with the necessary tools and knowledge to thrive in this new environment.
AI-Driven Career Tools in Manufacturing
AI career tools are becoming essential in the manufacturing sector as they facilitate personalized learning experiences and enhance workforce capabilities. These tools leverage data analytics and machine learning to identify skill gaps, recommend training programs, and provide real-time feedback. Here are some key AI-driven products that are shaping the future of factory worker training:
1. Smart Training Platforms
Platforms such as Skillsoft and Coursera for Business utilize AI algorithms to curate personalized learning paths for employees. By analyzing individual performance and preferences, these platforms can recommend specific courses that align with the worker’s career goals and the company’s needs. For instance, a factory worker aiming to transition from assembly line duties to a supervisory role can receive targeted training in leadership and advanced manufacturing technologies.
2. Virtual Reality (VR) and Augmented Reality (AR) Tools
VR and AR technologies, exemplified by tools like Praxar and STRIVR, offer immersive training experiences that enhance skill acquisition. These platforms simulate real-world factory environments, allowing workers to practice complex tasks without the risk of errors or accidents. For example, a worker can engage in a virtual assembly line, learning to operate machinery and troubleshoot issues in a controlled setting.
3. Predictive Analytics for Skill Development
AI-driven predictive analytics tools, such as IBM Watson, can analyze workforce data to forecast future skill requirements. By examining trends in production and market demands, these tools help organizations identify the competencies that will be essential in the coming years. This foresight enables companies to proactively upskill their workforce, ensuring they are prepared for technological advancements and industry shifts.
4. Chatbots and AI Mentors
AI chatbots and virtual mentors, like EdTech’s AI Tutor, provide on-demand support to factory workers. These tools can answer questions, provide troubleshooting guidance, and suggest training resources in real-time. This immediate access to information empowers workers to solve problems independently and enhances their learning experience.
Implementing AI in Workforce Training
To effectively implement AI-driven training tools, organizations should consider the following strategies:
1. Assess Current Skill Levels
Conduct a comprehensive skills assessment to identify existing competencies and gaps within the workforce. This data will inform the selection of appropriate AI tools and training programs.
2. Foster a Culture of Continuous Learning
Encourage a growth mindset among employees by promoting the importance of ongoing education and skill development. Highlighting success stories of upskilled workers can motivate others to engage with training programs.
3. Integrate AI Tools into Daily Operations
Incorporate AI-driven tools into the daily workflow of factory workers. This integration will allow employees to familiarize themselves with these technologies while enhancing their productivity and efficiency.
4. Monitor Progress and Adapt Training Programs
Utilize analytics from AI tools to monitor the progress of workers and the effectiveness of training programs. Regularly adapt training content and methods based on feedback and performance metrics to ensure continuous improvement.
Conclusion
As we approach 2025, the integration of AI in manufacturing is set to redefine the skill sets required for factory workers. By leveraging AI-driven career tools, organizations can effectively upskill their workforce, ensuring they remain competitive in an increasingly automated landscape. Embracing these technologies not only benefits the individual worker but also enhances overall operational efficiency and innovation within the manufacturing sector.
Keyword: AI upskilling for factory workers