Collaborative Robots and AI Transforming Manufacturing Workflows
Topic: AI Self Improvement Tools
Industry: Manufacturing and Industrial Automation
Discover how collaborative robots and AI are revolutionizing manufacturing workflows enhancing efficiency safety and cost-effectiveness in the industry
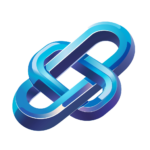
How Collaborative Robots and AI Are Transforming Manufacturing Workflows
The Rise of Collaborative Robots in Manufacturing
Collaborative robots, or cobots, are designed to work alongside human operators, enhancing productivity and safety in manufacturing environments. Unlike traditional industrial robots, which operate in isolation, cobots are built with advanced sensors and AI capabilities that allow them to interact seamlessly with human workers. This integration not only boosts efficiency but also fosters a more flexible manufacturing workflow.
Key Benefits of Collaborative Robots
- Increased Efficiency: Cobots can perform repetitive tasks with precision, allowing human workers to focus on more complex activities.
- Enhanced Safety: Equipped with safety features, cobots can operate safely in close proximity to humans, reducing workplace accidents.
- Cost-Effectiveness: Cobots are often less expensive than traditional robots, making them accessible for small to medium-sized enterprises.
Artificial Intelligence: The Brain Behind Automation
Artificial intelligence plays a crucial role in optimizing manufacturing workflows. By leveraging AI-driven tools, manufacturers can analyze vast amounts of data to improve decision-making and operational efficiency. AI algorithms can predict equipment failures, optimize supply chains, and enhance quality control processes.
Implementing AI in Manufacturing
To effectively implement AI in manufacturing, organizations can adopt various strategies:
- Data Collection: Implementing IoT devices to gather real-time data from machines and processes.
- Machine Learning: Utilizing machine learning algorithms to analyze data and identify patterns that can inform operational improvements.
- Predictive Maintenance: Employing AI tools to predict equipment failures before they occur, minimizing downtime and repair costs.
Examples of AI-Driven Tools in Manufacturing
Several AI-driven products are transforming manufacturing workflows:
- Siemens MindSphere: An IoT operating system that connects machines and physical infrastructure to the digital world, enabling manufacturers to analyze data for improved efficiency.
- IBM Watson: With its advanced data analytics capabilities, IBM Watson can help manufacturers optimize supply chains and enhance product quality through predictive analytics.
- Uptake: This AI-driven platform provides predictive maintenance solutions, helping manufacturers reduce unplanned downtime and extend the life of their equipment.
Case Studies: Success Stories in AI and Cobot Integration
Numerous companies have successfully integrated cobots and AI into their manufacturing processes:
- Ford Motor Company: Ford has implemented cobots in their assembly lines to assist workers with heavy lifting, significantly improving productivity while ensuring worker safety.
- General Electric: GE uses AI algorithms to analyze data from its manufacturing processes, leading to improved efficiency and reduced waste.
The Future of Manufacturing Workflows
The integration of collaborative robots and AI is not just a trend; it represents a fundamental shift in manufacturing workflows. As technology continues to evolve, manufacturers who embrace these innovations will be better positioned to compete in an increasingly complex global market.
Conclusion
In conclusion, the transformation of manufacturing workflows through collaborative robots and artificial intelligence is paving the way for a more efficient, safe, and cost-effective industry. By leveraging AI self-improvement tools and integrating cobots into their operations, manufacturers can enhance productivity and ensure long-term success in a rapidly changing landscape.
Keyword: collaborative robots in manufacturing