AI Tools Enhance Predictive Maintenance and Customer Service
Topic: AI Customer Service Tools
Industry: Manufacturing
Discover how AI tools enhance predictive maintenance and customer service in manufacturing for improved efficiency and stronger client relationships.
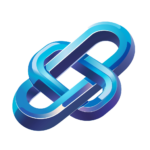
Predictive Maintenance Meets Customer Service: AI Tools for Proactive Support
In the rapidly evolving landscape of manufacturing, the integration of artificial intelligence (AI) into customer service processes is transforming how businesses operate. Predictive maintenance, a proactive approach to equipment management, is now being enhanced by AI-driven customer service tools, enabling manufacturers to not only maintain their machinery but also provide exceptional support to their clients.
The Role of AI in Predictive Maintenance
Predictive maintenance leverages data analytics and machine learning algorithms to forecast equipment failures before they occur. This approach minimizes downtime and reduces maintenance costs, ultimately leading to increased operational efficiency. By incorporating AI into predictive maintenance, manufacturers can analyze vast amounts of data collected from sensors and machinery to identify patterns and anomalies.
Data-Driven Insights
AI tools can process data from various sources, including IoT devices, historical maintenance records, and real-time performance metrics. By employing advanced algorithms, these tools can predict when a machine is likely to fail, allowing manufacturers to schedule maintenance before issues arise. This not only enhances equipment reliability but also improves customer satisfaction by ensuring that products are delivered on time and to specification.
Enhancing Customer Service with AI
In addition to predictive maintenance, AI tools are revolutionizing customer service in the manufacturing sector. By automating responses and providing personalized support, AI enhances the customer experience while reducing the workload on human agents.
AI-Driven Customer Support Tools
Several AI-driven products are making waves in the manufacturing industry, providing proactive support that aligns with predictive maintenance efforts. Here are a few notable examples:
- Chatbots: AI-powered chatbots, such as those developed by IBM Watson Assistant, can handle customer inquiries 24/7. They can provide instant responses to common questions about product specifications, troubleshooting, and maintenance schedules, freeing up human agents to focus on more complex issues.
- Predictive Analytics Platforms: Tools like Microsoft Azure AI offer predictive analytics capabilities that can be integrated into customer service platforms. These tools analyze customer data and predict future needs, allowing manufacturers to proactively reach out to customers with relevant information or support.
- Remote Monitoring Solutions: Companies such as GE Digital provide remote monitoring solutions that utilize AI to track equipment performance in real-time. By alerting customer service teams to potential issues, these solutions enable proactive outreach to customers, ensuring that any maintenance needs are addressed before they impact production.
Implementing AI Tools in Manufacturing
To successfully implement AI tools for predictive maintenance and customer service, manufacturers should consider the following steps:
1. Assess Current Infrastructure
Evaluate existing systems and data sources to determine how AI tools can be integrated. This includes assessing IoT devices, data management systems, and customer service platforms.
2. Choose the Right Tools
Select AI tools that align with your business goals and operational needs. Consider factors such as scalability, ease of integration, and the specific features that will enhance both predictive maintenance and customer service.
3. Train Staff
Invest in training for staff to ensure they are equipped to utilize AI tools effectively. This includes understanding how to interpret data insights and how to provide enhanced customer support leveraging AI capabilities.
4. Monitor and Optimize
Continuously monitor the performance of AI tools and gather feedback from both customers and staff. Use this information to optimize processes and improve the overall effectiveness of predictive maintenance and customer service efforts.
Conclusion
The convergence of predictive maintenance and customer service through AI tools presents a significant opportunity for manufacturers. By proactively addressing equipment issues and enhancing customer interactions, businesses can achieve greater operational efficiency and foster stronger relationships with their clients. As the manufacturing sector continues to embrace AI, those who leverage these technologies will undoubtedly gain a competitive edge in the marketplace.
Keyword: AI tools for predictive maintenance