Digital Twins Revolutionizing Factory Operations with AI Insights
Topic: AI Other Tools
Industry: Manufacturing
Discover how digital twins and AI are transforming factory operations by enhancing efficiency reducing downtime and improving decision-making in manufacturing
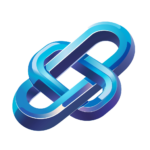
The Rise of Digital Twins: How Virtual Replicas are Transforming Factory Operations
Understanding Digital Twins
Digital twins are virtual replicas of physical assets, processes, or systems that leverage real-time data to simulate, predict, and optimize performance. In the manufacturing sector, these digital counterparts provide invaluable insights into factory operations, enabling companies to enhance efficiency, reduce downtime, and improve decision-making.
The Role of Artificial Intelligence in Digital Twins
Artificial Intelligence (AI) plays a pivotal role in the effectiveness of digital twins. By integrating AI algorithms with digital twin technology, manufacturers can analyze vast amounts of data generated from machines and processes. This analysis allows for predictive maintenance, real-time monitoring, and optimization of operations.
Implementing AI in Digital Twin Solutions
To successfully implement AI within digital twin solutions, manufacturers can follow these key steps:
- Data Collection: Utilize IoT sensors and devices to gather real-time data from machinery and production lines.
- Data Integration: Employ AI-driven platforms that can integrate disparate data sources into a cohesive system.
- Model Development: Create AI models that can simulate various scenarios based on the collected data.
- Continuous Learning: Implement machine learning algorithms that allow the digital twin to evolve and improve over time.
Examples of AI-Driven Tools for Digital Twins
Several AI-driven tools and products are available that can enhance the functionality of digital twins in manufacturing:
1. Siemens MindSphere
Siemens MindSphere is an industrial IoT as a service solution that connects physical products to the digital world. It enables manufacturers to create digital twins of their assets, allowing for real-time analytics and performance monitoring. By leveraging AI, users can predict equipment failures and optimize maintenance schedules.
2. PTC ThingWorx
PTC ThingWorx is a platform that provides tools for building and deploying digital twins. It incorporates machine learning capabilities to analyze data and provide actionable insights. This platform is particularly effective in improving product design and operational efficiency in manufacturing environments.
3. GE Digital’s Predix
Predix by GE Digital focuses on industrial data analytics and enables the creation of digital twins for industrial assets. With its AI capabilities, Predix can predict operational anomalies and suggest optimizations, thereby enhancing overall productivity.
Benefits of Digital Twins in Manufacturing
The adoption of digital twins in manufacturing presents numerous advantages:
- Enhanced Efficiency: By simulating operations, manufacturers can identify bottlenecks and streamline processes.
- Reduced Downtime: Predictive maintenance powered by AI helps in anticipating equipment failures before they occur.
- Improved Quality Control: Digital twins allow for continuous monitoring of production quality, enabling timely interventions.
- Cost Savings: Optimized operations lead to reduced waste and lower operational costs.
Conclusion
The rise of digital twins, augmented by artificial intelligence, is revolutionizing factory operations. By creating virtual replicas of physical assets, manufacturers can gain deeper insights into their processes, enhance efficiency, and drive innovation. As technology continues to evolve, the integration of AI with digital twins will likely lead to even more transformative changes in the manufacturing landscape.
Keyword: digital twins in manufacturing