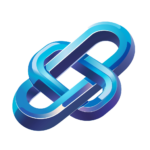
AI Driven Predictive Maintenance Workflow for Pharmaceutical Equipment
AI-driven predictive maintenance for pharmaceutical equipment enhances operational efficiency by utilizing real-time data analytics and machine learning for optimal performance
Category: AI App Tools
Industry: Pharmaceuticals
Predictive Maintenance for Pharmaceutical Equipment
1. Identify Equipment and Data Sources
1.1 Equipment Selection
Identify critical pharmaceutical equipment that requires maintenance, such as mixers, sterilizers, and packaging machines.
1.2 Data Source Identification
Determine data sources for the selected equipment, including sensors, historical maintenance logs, and operational data.
2. Data Collection and Integration
2.1 Sensor Installation
Install IoT sensors on equipment to monitor key performance indicators (KPIs) such as temperature, vibration, and pressure.
2.2 Data Aggregation
Utilize data integration tools like Apache Kafka to aggregate data from various sources into a centralized database.
3. Data Analysis and Model Development
3.1 Historical Data Analysis
Analyze historical maintenance and operational data to identify patterns and failure modes using AI tools.
3.2 Predictive Model Creation
Develop predictive models using machine learning algorithms (e.g., Random Forest, Neural Networks) with platforms like TensorFlow or PyTorch.
4. Implementation of AI Tools
4.1 AI-Driven Predictive Maintenance Tools
Implement AI-driven tools such as IBM Watson IoT or Siemens MindSphere to monitor equipment health in real-time.
4.2 Alert System Development
Establish an alert system that notifies maintenance teams of potential issues based on predictive model outputs.
5. Maintenance Scheduling and Execution
5.1 Maintenance Planning
Use AI insights to develop a proactive maintenance schedule that minimizes downtime and optimizes resource allocation.
5.2 Execution of Maintenance Tasks
Carry out maintenance tasks as per the schedule, ensuring documentation and feedback loops for continuous improvement.
6. Continuous Monitoring and Improvement
6.1 Performance Monitoring
Continuously monitor equipment performance using real-time data analytics to validate model predictions.
6.2 Model Refinement
Regularly update and refine predictive models based on new data and feedback from maintenance activities.
7. Reporting and Compliance
7.1 Generate Reports
Create detailed reports on maintenance activities, equipment performance, and predictive analytics insights for stakeholders.
7.2 Regulatory Compliance
Ensure all predictive maintenance practices comply with pharmaceutical regulations and standards, such as FDA guidelines.
Keyword: Predictive maintenance for pharmaceutical equipment