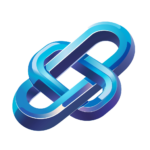
AI Driven Predictive Maintenance Workflow for Production Equipment
Discover how AI-driven predictive maintenance enhances production equipment efficiency reduces downtime and optimizes maintenance costs for better performance
Category: AI Beauty Tools
Industry: Personal Care Products
Predictive Maintenance for Production Equipment
1. Define Objectives
1.1 Identify Key Performance Indicators (KPIs)
Establish measurable goals for equipment efficiency, downtime reduction, and maintenance costs.
1.2 Set Maintenance Schedule
Determine frequency of maintenance checks based on production cycles and equipment usage.
2. Data Collection
2.1 Install Sensors
Equip production machinery with IoT sensors to monitor performance metrics such as temperature, vibration, and operational speed.
2.2 Aggregate Data
Utilize cloud-based platforms to collect and store data from all sensors in real-time for analysis.
3. Data Analysis
3.1 Implement AI Algorithms
Deploy machine learning algorithms to analyze historical data and identify patterns indicative of potential failures.
3.2 Predictive Analytics Tools
Utilize tools such as IBM Watson IoT or Microsoft Azure Machine Learning to generate predictive maintenance insights.
4. Maintenance Planning
4.1 Schedule Predictive Maintenance
Based on AI insights, create a proactive maintenance schedule to address potential issues before they lead to equipment failure.
4.2 Resource Allocation
Assign maintenance teams and allocate necessary resources based on the urgency and complexity of identified issues.
5. Execution of Maintenance
5.1 Perform Maintenance Tasks
Carry out scheduled maintenance activities, ensuring compliance with safety and operational standards.
5.2 Record Maintenance Activities
Document all maintenance actions taken, including parts replaced and time spent, for future reference.
6. Continuous Improvement
6.1 Review Performance Metrics
Analyze the impact of predictive maintenance on production efficiency and equipment reliability.
6.2 Update AI Models
Continuously refine AI algorithms with new data to improve predictive accuracy and adapt to changing production environments.
7. Feedback Loop
7.1 Gather Stakeholder Input
Solicit feedback from production teams regarding the effectiveness of predictive maintenance strategies.
7.2 Implement Changes
Make necessary adjustments to the workflow based on stakeholder feedback and performance analysis.
Keyword: Predictive maintenance for production equipment