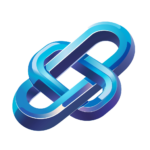
Robotic Arm Motion Planning with AI Integration Workflow
AI-driven robotic arm motion planning enhances efficiency through precise task definition data analysis and real-time control ensuring optimal performance and reliability
Category: AI Coding Tools
Industry: Robotics
Robotic Arm Motion Planning and Control
1. Define Objectives
1.1 Identify Task Requirements
Determine the specific tasks the robotic arm will perform, such as assembly, welding, or painting.
1.2 Establish Performance Metrics
Set criteria for success, including speed, precision, and reliability.
2. Data Collection and Analysis
2.1 Gather Environmental Data
Utilize sensors and cameras to collect data on the workspace and objects.
2.2 Analyze Data with AI Tools
Implement AI-driven analytics tools, such as TensorFlow or PyTorch, to process and interpret the collected data.
3. Motion Planning
3.1 Path Planning Algorithms
Apply algorithms like Rapidly-exploring Random Trees (RRT) or A* for determining optimal paths.
3.2 Simulation and Testing
Use simulation software such as Gazebo or V-REP to visualize and test motion plans before implementation.
4. Control System Development
4.1 Select Control Architecture
Choose between PID control, model predictive control, or reinforcement learning approaches.
4.2 Implement AI-Based Control
Integrate AI-driven products like ROS (Robot Operating System) for real-time control and feedback adjustments.
5. Integration and Calibration
5.1 Hardware Setup
Assemble the robotic arm and necessary peripherals, ensuring compatibility with control systems.
5.2 Calibration Procedures
Utilize AI tools to automate calibration processes, ensuring precision in motion execution.
6. Testing and Validation
6.1 Conduct Performance Tests
Run a series of tests to evaluate the arm’s performance against established metrics.
6.2 Analyze Results with AI Tools
Employ machine learning models to analyze test data and identify areas for improvement.
7. Deployment and Monitoring
7.1 Deploy in Operational Environment
Implement the robotic arm in its designated environment, ensuring all systems are functional.
7.2 Continuous Monitoring
Use AI-driven monitoring tools to track performance and make real-time adjustments as necessary.
8. Maintenance and Updates
8.1 Schedule Regular Maintenance
Establish a maintenance schedule to ensure long-term reliability and performance.
8.2 Update AI Models
Regularly retrain AI models with new data to enhance performance and adapt to changing conditions.
Keyword: Robotic arm motion planning