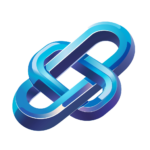
AI Enhanced Workflow for Aircraft Design Optimization
AI-assisted aircraft design optimization streamlines the design process through data analysis collaboration and advanced algorithms for enhanced performance and efficiency
Category: AI Collaboration Tools
Industry: Aerospace and Defense
AI-Assisted Aircraft Design Optimization
1. Initial Design Concept Development
1.1 Requirement Gathering
Identify and document the design requirements based on mission objectives, regulatory standards, and stakeholder inputs.
1.2 Conceptual Design Generation
Utilize AI-driven software such as Generative Design Tools (e.g., Autodesk Fusion 360) to explore multiple design iterations based on predefined parameters.
2. Data Collection and Analysis
2.1 Historical Data Compilation
Aggregate historical performance data from previous aircraft designs to inform the optimization process.
2.2 Simulation Data Generation
Employ AI simulation tools like ANSYS Discovery Live to create virtual prototypes and assess performance under various conditions.
3. Design Optimization
3.1 AI-Driven Optimization Algorithms
Implement machine learning algorithms, such as Genetic Algorithms and Neural Networks, to refine design parameters for improved performance and efficiency.
3.2 Multi-Objective Optimization
Utilize tools like MATLAB or COMSOL Multiphysics to balance trade-offs between conflicting objectives such as weight, cost, and aerodynamic efficiency.
4. Collaborative Review and Iteration
4.1 Team Collaboration Platforms
Facilitate collaboration among design teams using AI-enabled project management tools like Asana or Trello to track progress and gather feedback.
4.2 Design Review Sessions
Conduct regular design review meetings to discuss AI-generated insights and make iterative improvements based on team feedback.
5. Prototyping and Testing
5.1 Rapid Prototyping
Utilize AI-driven additive manufacturing technologies to create physical prototypes quickly for testing.
5.2 Performance Testing
Implement AI tools for real-time data analysis during testing phases, such as IBM Watson IoT, to monitor performance metrics and identify areas for further optimization.
6. Final Design Approval
6.1 Compliance Verification
Ensure the final design meets all regulatory and safety standards through AI compliance checking tools.
6.2 Stakeholder Presentation
Prepare a comprehensive presentation of the optimized design using visualization tools like Siemens NX to showcase the benefits achieved through AI assistance.
7. Implementation and Production Planning
7.1 Production Readiness Assessment
Conduct a final assessment using AI analytics to ensure readiness for production.
7.2 Supply Chain Optimization
Leverage AI supply chain management tools such as SAP Integrated Business Planning to optimize material procurement and production scheduling.
8. Post-Implementation Review
8.1 Performance Monitoring
Utilize AI monitoring tools to track the performance of the aircraft post-deployment and gather data for future design improvements.
8.2 Continuous Improvement Cycle
Establish a feedback loop where insights gained from operational data inform future design iterations and enhancements.
Keyword: AI aircraft design optimization