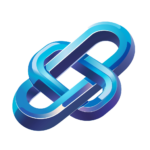
AI Integration for Predictive Maintenance in Food Processing
AI-driven predictive maintenance enhances food processing by identifying critical equipment monitoring performance data and ensuring compliance with safety standards
Category: AI Cooking Tools
Industry: Food Safety and Quality Control
AI-Driven Predictive Maintenance for Food Processing Equipment
1. Identify Critical Equipment
1.1 Inventory Assessment
Conduct a thorough inventory of all food processing equipment to identify critical assets that impact food safety and quality.
1.2 Risk Analysis
Perform a risk analysis to determine which equipment is most susceptible to failure and has the highest impact on production quality.
2. Data Collection
2.1 Sensor Installation
Install IoT sensors on critical equipment to monitor key performance indicators (KPIs) such as temperature, humidity, and vibration.
2.2 Data Aggregation
Utilize data aggregation tools to collect real-time data from sensors and existing maintenance logs.
3. Data Analysis
3.1 AI Model Development
Develop machine learning models to analyze historical data and predict equipment failures. Tools such as TensorFlow or PyTorch can be employed for model training.
3.2 Predictive Analytics
Implement predictive analytics platforms like IBM Watson or Microsoft Azure Machine Learning to interpret data and generate actionable insights.
4. Maintenance Scheduling
4.1 Predictive Maintenance Alerts
Set up automated alerts for maintenance teams when AI models predict potential failures or maintenance needs.
4.2 Maintenance Planning
Utilize scheduling software such as CMMS (Computerized Maintenance Management System) to plan and prioritize maintenance activities based on AI insights.
5. Implementation of AI-Driven Tools
5.1 AI Cooking Tools
Integrate AI cooking tools that monitor cooking parameters in real-time to ensure food safety and quality. Examples include smart ovens that adjust cooking times based on sensor data.
5.2 Quality Control Systems
Employ AI-driven quality control systems like Plate IQ to analyze food quality and safety data, ensuring compliance with industry standards.
6. Continuous Improvement
6.1 Feedback Loop
Establish a feedback loop where maintenance outcomes are analyzed to refine AI models and improve predictive accuracy.
6.2 Training and Development
Provide ongoing training for staff on new AI tools and predictive maintenance practices to enhance operational efficiency.
7. Reporting and Compliance
7.1 Data Reporting
Generate regular reports on equipment performance, maintenance activities, and compliance with food safety regulations.
7.2 Regulatory Compliance
Ensure adherence to food safety standards by utilizing AI-driven documentation tools that maintain accurate records of maintenance and inspections.
Keyword: AI predictive maintenance food processing