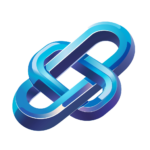
AI Driven Equipment Lifespan Prediction and Replacement Workflow
AI-driven workflow for equipment lifespan prediction and replacement scheduling enhances operational efficiency through data collection predictive analytics and continuous improvement
Category: AI Data Tools
Industry: Manufacturing
Equipment Lifespan Prediction and Replacement Scheduling
1. Data Collection
1.1 Identify Equipment
Catalog all manufacturing equipment and machinery, including specifications, usage history, and maintenance records.
1.2 Gather Operational Data
Utilize IoT sensors and monitoring tools to collect real-time operational data such as temperature, vibration, and usage hours.
1.3 Historical Performance Analysis
Compile historical performance data to understand past failures and maintenance interventions.
2. Data Processing
2.1 Data Cleaning
Implement data cleaning techniques to ensure accuracy and consistency in the dataset.
2.2 Data Integration
Integrate data from various sources using platforms like Apache Kafka or Microsoft Azure Data Factory.
3. Predictive Analytics
3.1 AI Model Development
Develop machine learning models using tools such as TensorFlow or PyTorch to predict equipment lifespan based on collected data.
3.2 Feature Engineering
Identify key features that influence equipment lifespan, such as operational load and environmental conditions.
3.3 Model Training and Validation
Train the predictive models with historical data and validate their accuracy using techniques like cross-validation.
4. Prediction and Analysis
4.1 Lifespan Prediction
Utilize the trained AI models to predict the remaining useful life (RUL) of each piece of equipment.
4.2 Risk Assessment
Conduct a risk assessment based on predicted lifespan to identify critical equipment that may require immediate attention.
5. Replacement Scheduling
5.1 Develop Replacement Strategy
Create a replacement strategy based on predicted lifespan, operational needs, and budget considerations.
5.2 Schedule Maintenance and Replacement
Use scheduling software such as SAP PM or IBM Maximo to plan maintenance and replacement activities effectively.
6. Continuous Improvement
6.1 Monitor and Update Models
Continuously monitor equipment performance and update AI models with new data to improve prediction accuracy.
6.2 Feedback Loop
Establish a feedback loop to incorporate insights from maintenance teams and operational staff into the predictive models.
7. Reporting and Documentation
7.1 Generate Reports
Create detailed reports on equipment lifespan predictions and maintenance schedules for stakeholders.
7.2 Documentation of Processes
Document the workflow process and any changes made to ensure compliance and facilitate training for new staff.
Keyword: equipment lifespan prediction