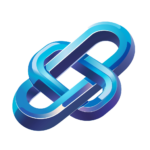
AI Driven Generative Design Workflow for Aerospace Components
Discover how AI-driven generative design transforms aerospace component development through data analysis simulation and continuous improvement for optimal performance
Category: AI Data Tools
Industry: Aerospace and Defense
Generative Design for Aerospace Components
1. Define Project Objectives
1.1 Identify Requirements
Gather specifications for the aerospace components, including weight, strength, and material constraints.
1.2 Establish Performance Metrics
Determine key performance indicators (KPIs) such as cost, durability, and manufacturability.
2. Data Collection and Preparation
2.1 Gather Historical Data
Utilize AI-driven tools to collect historical performance data from existing aerospace components.
- Example Tool: Siemens Mindsphere – for data analytics and IoT integration.
2.2 Clean and Organize Data
Implement data cleaning techniques to ensure accuracy and reliability of input data.
- Example Tool: Alteryx – for data preparation and blending.
3. Generative Design Process
3.1 Setup Generative Design Software
Choose appropriate generative design software that integrates AI capabilities.
- Example Tool: Autodesk Fusion 360 – for generative design simulations.
3.2 Input Design Parameters
Input the defined requirements and constraints into the software.
3.3 Run Generative Design Algorithms
Leverage AI algorithms to explore multiple design alternatives based on the input parameters.
- Example Tool: nTopology – for advanced lattice structures and complex geometries.
4. Analyze Generated Designs
4.1 Evaluate Performance
Use simulation tools to assess the performance of generated designs against established KPIs.
- Example Tool: ANSYS – for finite element analysis and simulation.
4.2 Select Optimal Design
Identify the design that meets or exceeds performance metrics and is feasible for manufacturing.
5. Prototype Development
5.1 Create Prototypes
Utilize additive manufacturing techniques to create prototypes of the selected design.
- Example Tool: Stratasys – for 3D printing solutions.
5.2 Conduct Testing
Perform physical testing on prototypes to validate performance and identify any design flaws.
6. Final Design Iteration
6.1 Implement Feedback
Analyze testing results and refine the design as necessary.
6.2 Finalize Design for Production
Prepare the final design for manufacturing, ensuring compliance with aerospace standards.
7. Production and Quality Assurance
7.1 Manufacturing Setup
Coordinate with manufacturing teams to initiate production of the final design.
7.2 Quality Control
Utilize AI-driven quality assurance tools to monitor production quality.
- Example Tool: MachineMetrics – for real-time production monitoring.
8. Post-Production Analysis
8.1 Gather Performance Data
Collect data from the produced components to evaluate performance in real-world applications.
8.2 Continuous Improvement
Implement a feedback loop to inform future design iterations and enhance the generative design process.
Keyword: Generative design for aerospace components