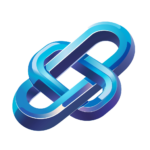
AI Driven Workflow for 3D Model Optimization with Machine Learning
AI-driven workflow optimizes 3D model creation through machine learning enhancing print quality and reducing waste while ensuring continuous improvement and collaboration
Category: AI Design Tools
Industry: 3D Printing and Prototyping
Machine Learning-Powered 3D Model Optimization
1. Initial Model Creation
1.1 Design Phase
Utilize CAD software to create initial 3D models. Tools such as Autodesk Fusion 360 or SolidWorks can be employed for precise modeling.
1.2 Exporting Models
Export the designed models in compatible formats (e.g., STL, OBJ) for further processing.
2. Data Collection and Preparation
2.1 Gathering Historical Data
Collect data from previous 3D printing projects, including successful prints, failures, and material performance metrics.
2.2 Data Cleaning
Utilize data preprocessing tools such as Python’s Pandas library to clean and organize the collected data for analysis.
3. Machine Learning Model Development
3.1 Feature Selection
Identify key features that influence print quality, such as layer height, infill percentage, and material type.
3.2 Model Training
Employ machine learning frameworks like TensorFlow or PyTorch to train predictive models that optimize 3D printing parameters based on historical data.
3.3 Model Validation
Validate the model using cross-validation techniques to ensure accuracy and reliability of predictions.
4. Optimization Process
4.1 Parameter Optimization
Use the trained machine learning model to suggest optimal printing parameters for new designs, enhancing print quality and reducing material waste.
4.2 Simulation and Testing
Run simulations using tools like ANSYS or Autodesk Netfabb to predict the performance of the optimized models before actual printing.
5. Implementation of AI-Driven Tools
5.1 AI Design Assistance
Incorporate AI-driven design tools such as nTopology or Frustum, which leverage generative design to create optimized structures automatically.
5.2 Continuous Learning
Implement feedback loops where the outcomes of printed prototypes are fed back into the machine learning model to continuously improve optimization.
6. Final Output and Review
6.1 Print Preparation
Prepare the final optimized model for printing using slicing software like Ultimaker Cura or PrusaSlicer.
6.2 Quality Assurance
Conduct a final review of the model and parameters to ensure all specifications meet the required standards for production.
7. Post-Production Analysis
7.1 Performance Evaluation
Evaluate the printed prototype against desired criteria (e.g., strength, flexibility, accuracy) and document the results.
7.2 Feedback Integration
Gather feedback from stakeholders and integrate insights into the training dataset for future model improvements.
8. Documentation and Reporting
8.1 Report Generation
Create a comprehensive report detailing the optimization process, parameters used, and performance outcomes.
8.2 Knowledge Sharing
Share findings with the team and stakeholders to promote best practices and enhance collaborative efforts in future projects.
Keyword: 3D model optimization with AI