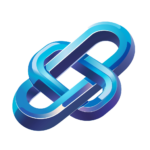
AI Driven Predictive Maintenance Workflow for Power Plants
AI-driven predictive maintenance for power plants enhances efficiency by utilizing real-time data analysis to prevent equipment failures and optimize maintenance scheduling
Category: AI Developer Tools
Industry: Energy and Utilities
Predictive Maintenance for Power Plants
1. Data Collection
1.1 Sensor Data Acquisition
Utilize IoT sensors to collect real-time data from equipment such as turbines, generators, and boilers. This includes temperature, vibration, and pressure readings.
1.2 Historical Data Gathering
Compile historical maintenance records and operational data to establish baseline performance metrics. This data can be sourced from existing databases or enterprise resource planning (ERP) systems.
2. Data Processing
2.1 Data Cleaning
Implement data preprocessing techniques to remove noise and outliers from the collected data, ensuring high-quality input for analysis.
2.2 Data Integration
Integrate data from various sources, including SCADA systems and enterprise databases, to create a unified dataset for analysis.
3. AI Model Development
3.1 Feature Engineering
Identify and create relevant features that contribute to predictive maintenance, such as failure rates and operational conditions.
3.2 Model Selection
Select appropriate machine learning algorithms for predictive analysis, such as Random Forest, Support Vector Machines, or Neural Networks.
3.3 Model Training
Utilize AI development tools such as TensorFlow or PyTorch to train models on the processed data, optimizing for accuracy and performance.
4. Prediction and Analysis
4.1 Predictive Analytics
Deploy the trained models to predict potential equipment failures and maintenance needs. This can be facilitated through platforms like IBM Watson or Azure Machine Learning.
4.2 Risk Assessment
Analyze the predictions to assess risks and prioritize maintenance tasks based on urgency and impact on operations.
5. Maintenance Planning
5.1 Scheduling
Leverage predictive insights to create a proactive maintenance schedule that minimizes downtime and optimizes resource allocation.
5.2 Resource Allocation
Utilize AI-driven tools like SAP Intelligent Asset Management to allocate resources effectively, ensuring that the right personnel and materials are available for maintenance tasks.
6. Implementation and Monitoring
6.1 Execution of Maintenance Tasks
Carry out maintenance activities as per the schedule, ensuring adherence to safety and operational standards.
6.2 Continuous Monitoring
Continue to monitor equipment performance post-maintenance using real-time data analytics tools such as Splunk or Google Cloud Operations Suite.
7. Feedback Loop
7.1 Performance Evaluation
Evaluate the effectiveness of maintenance strategies and model predictions through key performance indicators (KPIs) such as equipment uptime and maintenance costs.
7.2 Model Refinement
Refine AI models based on feedback and new data to improve accuracy and adapt to changing operational conditions.
8. Reporting and Documentation
8.1 Reporting
Generate detailed reports on maintenance activities, predictive analytics insights, and overall equipment performance for stakeholders.
8.2 Documentation
Maintain comprehensive documentation of processes, model iterations, and maintenance outcomes to support ongoing improvement initiatives.
Keyword: Predictive maintenance for power plants