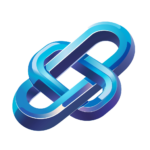
AI Driven Predictive Maintenance Workflow for Production Equipment
Discover AI-driven predictive maintenance for production equipment with real-time data collection model development and proactive maintenance scheduling
Category: AI Domain Tools
Industry: Automotive
Predictive Maintenance for Production Equipment
1. Data Collection
1.1 Sensor Installation
Install IoT sensors on production equipment to gather real-time data on performance metrics such as temperature, vibration, and operational speed.
1.2 Data Aggregation
Utilize cloud-based platforms like AWS IoT or Microsoft Azure IoT Hub to aggregate data from multiple sensors for centralized access.
2. Data Processing
2.1 Data Cleaning
Implement data preprocessing techniques to clean and filter the collected data, ensuring accuracy for analysis.
2.2 Feature Engineering
Identify and create relevant features from raw data that can enhance the predictive capabilities of AI models.
3. Model Development
3.1 Algorithm Selection
Choose appropriate machine learning algorithms such as Random Forest, Support Vector Machines, or Deep Learning models for predictive analysis.
3.2 Tool Utilization
Employ AI-driven tools such as TensorFlow, PyTorch, or IBM Watson to build and train predictive maintenance models.
4. Model Training and Validation
4.1 Training
Train the selected models using historical data to recognize patterns indicative of equipment failure.
4.2 Validation
Validate model accuracy through techniques such as cross-validation and performance metrics assessment (e.g., precision, recall).
5. Deployment
5.1 Integration with Production Systems
Integrate the predictive maintenance model into existing production management systems for real-time monitoring and alerts.
5.2 AI-Driven Dashboards
Utilize visualization tools like Tableau or Power BI to create dashboards that present predictive insights and maintenance schedules to stakeholders.
6. Monitoring and Feedback
6.1 Continuous Monitoring
Continuously monitor equipment performance and model predictions to ensure accuracy and reliability.
6.2 Feedback Loop
Establish a feedback loop to refine models based on new data and maintenance outcomes, enhancing predictive capabilities over time.
7. Maintenance Execution
7.1 Proactive Maintenance Scheduling
Utilize predictive insights to schedule maintenance activities proactively, reducing downtime and extending equipment lifespan.
7.2 Documentation and Reporting
Document maintenance activities and outcomes for future analysis and compliance purposes, using tools like SAP or Oracle for record-keeping.
Keyword: Predictive maintenance for equipment