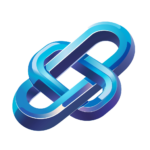
Automated Visual Inspection Workflow with AI Integration
Optimize manufacturing quality control with an AI-driven automated visual inspection workflow ensuring product consistency and reducing defects efficiently
Category: AI Domain Tools
Industry: Manufacturing
Automated Visual Inspection Workflow
1. Objective
To implement an efficient automated visual inspection system utilizing AI-driven tools to enhance quality control in manufacturing processes.
2. Workflow Overview
This workflow outlines the steps involved in setting up and executing an automated visual inspection system, leveraging artificial intelligence to ensure product quality and consistency.
3. Workflow Steps
Step 1: Requirement Analysis
Identify the specific requirements for visual inspection based on product specifications and quality standards.
- Define inspection criteria (e.g., dimensions, color, surface defects).
- Determine the volume of products to be inspected.
Step 2: Tool Selection
Select appropriate AI-driven tools for visual inspection.
- Computer Vision Software: Tools like OpenCV or TensorFlow can be utilized for image processing.
- Machine Learning Models: Implement models such as Convolutional Neural Networks (CNNs) for defect detection.
- Inspection Hardware: Utilize high-resolution cameras and lighting systems to capture images.
Step 3: Data Collection
Gather data for training AI models.
- Collect images of products with both acceptable and defective examples.
- Label the data accurately for supervised learning.
Step 4: Model Training
Train the AI model using the collected data.
- Use frameworks such as PyTorch or Keras to develop and train the model.
- Evaluate model performance using metrics like accuracy and recall.
Step 5: System Integration
Integrate the trained AI model into the manufacturing line.
- Connect the visual inspection system to the production line for real-time analysis.
- Ensure compatibility with existing manufacturing execution systems (MES).
Step 6: Testing and Calibration
Conduct thorough testing and calibration of the system.
- Run pilot tests with a sample of products to validate the inspection results.
- Calibrate the system based on feedback and performance metrics.
Step 7: Deployment
Deploy the automated visual inspection system across the production line.
- Train staff on system operation and troubleshooting.
- Implement a monitoring system for ongoing performance evaluation.
Step 8: Continuous Improvement
Establish a feedback loop for continuous improvement.
- Regularly update the AI model with new data to enhance accuracy.
- Analyze inspection results to identify areas for process improvement.
4. Conclusion
The successful implementation of an automated visual inspection system can significantly improve product quality and operational efficiency in manufacturing. By leveraging AI-driven tools, manufacturers can ensure consistent quality control and reduce the risk of defects.
Keyword: automated visual inspection system