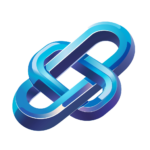
Automated Cost Analysis with AI for Optimization Workflow
Automated cost analysis and optimization leverages AI for data collection preprocessing analysis and reporting to enhance efficiency and reduce costs in manufacturing
Category: AI Finance Tools
Industry: Manufacturing
Automated Cost Analysis and Optimization
1. Data Collection
1.1 Identify Data Sources
Determine relevant data sources including ERP systems, production databases, and financial records.
1.2 Data Extraction
Utilize ETL (Extract, Transform, Load) tools such as Talend or Apache Nifi to gather data from identified sources.
2. Data Preprocessing
2.1 Data Cleaning
Implement data cleaning techniques to remove duplicates and correct inconsistencies using tools like OpenRefine.
2.2 Data Transformation
Transform data into a suitable format for analysis using Python libraries (e.g., Pandas) or R.
3. Cost Analysis
3.1 Cost Attribution
Use AI algorithms to allocate costs accurately across various manufacturing processes. Tools like IBM Watson Analytics can assist in this phase.
3.2 Cost Benchmarking
Employ AI-driven benchmarking tools such as CostPerform to compare costs against industry standards.
4. Optimization Modeling
4.1 Predictive Analysis
Implement machine learning models to predict future costs based on historical data using platforms like Google Cloud AI or Azure Machine Learning.
4.2 Scenario Simulation
Utilize simulation tools such as AnyLogic to model different manufacturing scenarios and their financial implications.
5. Reporting and Visualization
5.1 Dashboard Creation
Develop interactive dashboards using BI tools like Tableau or Power BI to visualize cost analysis results.
5.2 Reporting Automation
Automate reporting processes with tools like Microsoft Power Automate to ensure timely delivery of insights to stakeholders.
6. Continuous Improvement
6.1 Feedback Loop
Establish a feedback loop to gather insights from users and stakeholders for ongoing refinement of the analysis process.
6.2 AI Model Retraining
Regularly retrain AI models with new data to enhance predictive accuracy and adapt to changing manufacturing conditions.
7. Implementation of Recommendations
7.1 Action Plan Development
Create actionable plans based on analysis results, focusing on cost-saving measures and efficiency improvements.
7.2 Stakeholder Engagement
Engage relevant stakeholders to ensure alignment and support for the implementation of recommendations.
Keyword: automated cost analysis tools