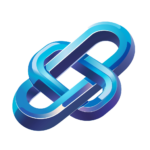
AI Integration for Efficient Paint and Surface Defect Detection
AI-assisted workflow enhances paint and surface defect detection in automotive manufacturing improving quality control and reducing production costs
Category: AI Image Tools
Industry: Automotive
AI-Assisted Paint and Surface Defect Detection
1. Workflow Overview
This workflow outlines the process of utilizing artificial intelligence (AI) for detecting paint and surface defects in automotive applications. The integration of AI image tools enhances the efficiency and accuracy of defect detection, leading to improved quality control and reduced production costs.
2. Workflow Steps
Step 1: Data Collection
Gather a comprehensive dataset of images showcasing various paint and surface defects. This dataset should include:
- High-resolution images of vehicles with known defects.
- Images of vehicles in different lighting and environmental conditions.
- Annotated data indicating the type and location of defects.
Step 2: Data Preprocessing
Prepare the collected images for analysis by performing the following:
- Image normalization to ensure consistency in lighting and color.
- Data augmentation techniques such as rotation, scaling, and flipping to enhance the dataset.
- Segmentation of images to isolate areas of interest, focusing on paint and surface regions.
Step 3: Model Selection and Training
Select appropriate AI models for defect detection, such as:
- Convolutional Neural Networks (CNNs): Ideal for image classification and feature extraction.
- Generative Adversarial Networks (GANs): Useful for generating synthetic images to augment training data.
Train the selected models using the preprocessed dataset, employing techniques like:
- Transfer learning to leverage pre-trained models.
- Hyperparameter tuning to optimize model performance.
Step 4: Model Evaluation
Assess the performance of the trained models through:
- Confusion matrices to evaluate classification accuracy.
- Precision, recall, and F1-score metrics for comprehensive analysis.
- Cross-validation to ensure model robustness across different datasets.
Step 5: Deployment
Implement the trained AI model into the production environment using tools such as:
- TensorFlow Serving: For serving machine learning models in production.
- OpenCV: For real-time image processing and defect detection.
Integrate the AI system with existing quality control processes to automate defect detection.
Step 6: Real-Time Monitoring and Feedback
Utilize AI-driven dashboards for:
- Real-time monitoring of defect detection results.
- Providing feedback to production teams for immediate action.
- Collecting data on defect types and frequencies for future analysis.
Step 7: Continuous Improvement
Establish a feedback loop to:
- Regularly update the dataset with new images and defect types.
- Retrain models periodically to improve accuracy and adapt to new conditions.
- Incorporate user feedback to enhance the AI system’s functionality.
3. Conclusion
By implementing this AI-assisted workflow for paint and surface defect detection, automotive manufacturers can achieve higher quality standards, reduce inspection times, and minimize costs associated with defects. The utilization of advanced AI tools and techniques will foster a more efficient production environment.
Keyword: AI paint defect detection system