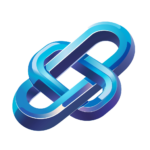
Real Time AI Defect Detection Workflow for Production Lines
AI-driven workflow enhances real-time defect detection on production lines improving quality control reducing waste and boosting efficiency in manufacturing processes
Category: AI Image Tools
Industry: Manufacturing
Real-Time Defect Detection on Production Lines
1. Workflow Overview
This workflow outlines the steps involved in implementing AI image tools for real-time defect detection on manufacturing production lines. The goal is to enhance quality control and reduce waste by leveraging advanced technologies.
2. Initial Setup
2.1 Define Objectives
Identify specific quality control goals, such as reducing defect rates and improving inspection speed.
2.2 Select AI Image Tools
Choose appropriate AI-driven tools based on production needs. Examples include:
- Computer Vision Systems: Tools like Cognex VisionPro and Siemens Inspector for image processing and defect identification.
- Machine Learning Platforms: Utilize platforms such as TensorFlow or Pytorch for training custom models.
3. Data Acquisition
3.1 Image Capture
Install high-resolution cameras on the production line to capture images of products at various stages.
3.2 Data Collection
Gather a diverse dataset of images, including both defective and non-defective items, to train the AI models effectively.
4. Model Development
4.1 Data Annotation
Label the collected images to indicate defects, using tools like Labelbox or VGG Image Annotator.
4.2 Train AI Models
Employ selected machine learning platforms to develop and train models on the annotated dataset.
4.3 Validate Model Performance
Test the models against a validation dataset to ensure accuracy and reliability in defect detection.
5. Implementation on Production Line
5.1 Integrate AI Systems
Deploy the trained models into the production line environment, integrating with existing quality control systems.
5.2 Real-Time Monitoring
Utilize real-time image analysis to detect defects during production, with tools like OpenCV for processing images on-the-fly.
6. Feedback Loop
6.1 Continuous Learning
Implement a feedback mechanism to continuously improve model accuracy by retraining with new data collected from production.
6.2 Performance Metrics
Monitor key performance indicators (KPIs), such as defect detection rate and false positive rate, to assess the system’s effectiveness.
7. Reporting and Analysis
7.1 Generate Reports
Create regular reports summarizing defect detection performance, using tools like Tableau or Power BI for visualization.
7.2 Review and Optimize
Conduct periodic reviews of the system and make adjustments based on performance data and feedback from production staff.
8. Conclusion
By implementing a structured workflow for real-time defect detection using AI image tools, manufacturers can significantly enhance quality control processes, reduce waste, and improve overall production efficiency.
Keyword: AI defect detection workflow