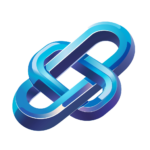
AI Driven Predictive Maintenance Workflow for Utility Infrastructure
AI-driven predictive maintenance for utility infrastructure enhances efficiency through real-time data collection analysis monitoring and proactive repairs for optimal performance
Category: AI News Tools
Industry: Energy and Utilities
Predictive Maintenance for Utility Infrastructure
1. Data Collection
1.1 Sensor Deployment
Install IoT sensors across utility infrastructure to gather real-time data on equipment performance, environmental conditions, and operational metrics.
1.2 Historical Data Aggregation
Compile historical maintenance records, failure reports, and operational data to create a comprehensive dataset for analysis.
2. Data Processing and Analysis
2.1 Data Cleaning
Utilize AI-driven tools such as DataRobot or Tableau to clean and preprocess the collected data, ensuring accuracy and consistency.
2.2 Predictive Analytics
Implement machine learning algorithms using platforms like IBM Watson or Microsoft Azure Machine Learning to analyze data and identify patterns that indicate potential failures.
3. Condition Monitoring
3.1 Real-Time Monitoring
Use AI-powered monitoring systems such as Predictive Maintenance by Siemens or GE Digital’s Predix to track equipment health and performance continuously.
3.2 Anomaly Detection
Employ AI algorithms to detect anomalies in equipment performance, enabling early identification of issues before they escalate into failures.
4. Maintenance Scheduling
4.1 Predictive Maintenance Alerts
Set up automated alerts through AI systems that notify maintenance teams when predictive analytics indicate a high likelihood of equipment failure.
4.2 Resource Allocation
Utilize AI tools such as UpKeep or Fiix for optimizing resource allocation and scheduling maintenance tasks based on predictive insights.
5. Implementation of Maintenance Actions
5.1 Proactive Repairs
Conduct maintenance activities based on AI-driven insights, addressing potential failures before they impact operations.
5.2 Performance Review
After maintenance actions, review equipment performance using AI analytics to assess the effectiveness of the interventions.
6. Continuous Improvement
6.1 Feedback Loop
Incorporate feedback from maintenance outcomes into the AI models to enhance predictive accuracy and adapt to changing operational conditions.
6.2 Training and Development
Provide ongoing training for staff on the use of AI tools and the importance of data-driven maintenance strategies to foster a culture of continuous improvement.
Keyword: Predictive maintenance for utilities