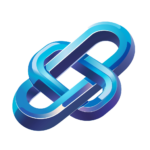
AI Powered Generative Design Workflow for Aircraft Optimization
Discover AI-driven generative design optimization for aircraft components enhancing performance and compliance through innovative workflows and advanced technologies
Category: AI Other Tools
Industry: Aerospace and Defense
Generative Design Optimization for Aircraft Components
1. Define Design Requirements
1.1 Identify Performance Criteria
Establish key parameters such as weight, strength, durability, and cost.
1.2 Gather Regulatory Standards
Ensure compliance with aviation industry regulations and safety standards.
2. Data Collection and Preparation
2.1 Collect Historical Data
Utilize existing data on previous aircraft components to inform design.
2.2 Implement Data Cleaning Tools
Use AI-driven data cleaning tools such as DataRobot or Trifacta to ensure data integrity.
3. Generative Design Process
3.1 Select Generative Design Software
Choose appropriate software tools such as Autodesk Fusion 360 or Siemens NX that incorporate AI algorithms.
3.2 Input Design Parameters
Feed the defined requirements and constraints into the generative design software.
3.3 Generate Design Alternatives
Utilize AI algorithms to create multiple design options based on input parameters.
4. Simulation and Analysis
4.1 Conduct Finite Element Analysis (FEA)
Use tools like ANSYS or Abaqus to simulate performance under various conditions.
4.2 Evaluate Design Options
Assess the generated designs based on performance metrics and regulatory compliance.
5. Optimization and Refinement
5.1 Apply AI-Driven Optimization Tools
Use optimization software such as Altair HyperWorks or COMSOL Multiphysics to refine the best design options.
5.2 Iterate Based on Feedback
Incorporate feedback from engineers and stakeholders to further enhance designs.
6. Prototype Development
6.1 Select Manufacturing Method
Determine the most suitable manufacturing techniques such as additive manufacturing or CNC machining.
6.2 Create Prototypes
Utilize rapid prototyping tools to develop physical models of the optimized designs.
7. Testing and Validation
7.1 Conduct Performance Testing
Perform rigorous testing to validate the prototypes against the defined performance criteria.
7.2 Analyze Test Results
Utilize AI analytics tools to interpret test data and identify areas for improvement.
8. Final Design Approval
8.1 Review by Stakeholders
Present final designs to stakeholders for approval, ensuring all requirements are met.
8.2 Document the Design Process
Compile comprehensive documentation of the design and optimization process for future reference.
9. Implementation and Production
9.1 Transition to Production
Coordinate with manufacturing teams to begin production of the approved designs.
9.2 Monitor Production Quality
Implement AI-driven quality control systems to ensure adherence to specifications throughout production.
Keyword: Generative design optimization aircraft components