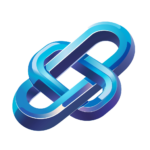
AI Driven Predictive Maintenance Workflow for Food Service Equipment
AI-driven predictive maintenance for food service equipment enhances efficiency through data collection analysis scheduling monitoring and continuous improvement
Category: AI Sales Tools
Industry: Food and Beverage
Predictive Maintenance for Food Service Equipment
1. Data Collection
1.1 Identify Equipment
Catalog all food service equipment that requires monitoring, including ovens, refrigerators, fryers, and dishwashers.
1.2 Sensor Installation
Install IoT sensors on each piece of equipment to collect real-time data on performance metrics such as temperature, humidity, and operational hours.
1.3 Data Integration
Integrate collected data into a centralized system using platforms like Microsoft Azure or AWS IoT Core for seamless access and analysis.
2. Data Analysis
2.1 AI Model Development
Utilize machine learning algorithms to analyze historical performance data and identify patterns that indicate potential equipment failures.
2.2 Predictive Analytics Tools
Implement AI-driven tools such as IBM Watson or Google Cloud AI to enhance predictive capabilities and forecast maintenance needs based on analyzed data.
3. Maintenance Scheduling
3.1 Automated Alerts
Set up an automated alert system that notifies maintenance personnel when equipment performance falls below predetermined thresholds.
3.2 Maintenance Planning
Utilize AI scheduling tools like UpKeep or Fiix to efficiently plan and allocate resources for preventive maintenance tasks.
4. Performance Monitoring
4.1 Continuous Monitoring
Continuously monitor equipment performance through dashboards that display real-time data and predictive insights.
4.2 Feedback Loop
Establish a feedback mechanism to refine AI models based on maintenance outcomes and equipment performance post-service.
5. Reporting and Optimization
5.1 Generate Reports
Create detailed reports on maintenance activities, equipment performance, and predictive accuracy to assess overall effectiveness.
5.2 Process Optimization
Utilize insights gained from reporting to optimize the predictive maintenance process, ensuring alignment with operational goals and cost efficiency.
6. Continuous Improvement
6.1 Training and Development
Provide ongoing training for staff on the use of AI tools and the importance of predictive maintenance in enhancing operational efficiency.
6.2 Technology Updates
Regularly review and update AI tools and technologies to incorporate the latest advancements in predictive analytics and IoT.
Keyword: Predictive maintenance for food equipment