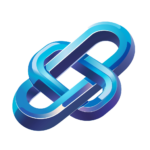
AI Driven Predictive Maintenance Workflow for Logistics Equipment
Discover how AI-driven predictive maintenance enhances logistics equipment efficiency through data collection analysis insights and continuous improvement strategies
Category: AI Search Tools
Industry: Logistics and Supply Chain
Predictive Maintenance for Logistics Equipment
1. Data Collection
1.1 Identify Equipment
Catalog all logistics equipment requiring predictive maintenance, including forklifts, conveyor systems, and delivery vehicles.
1.2 Sensor Installation
Install IoT sensors on identified equipment to gather real-time data on operational performance, temperature, vibration, and usage patterns.
1.3 Data Aggregation
Utilize cloud-based platforms to aggregate data from various sources, ensuring a centralized repository for analysis.
2. Data Analysis
2.1 AI Model Development
Develop machine learning models using historical maintenance data to predict potential equipment failures. Tools such as TensorFlow or PyTorch can be employed for model training.
2.2 Anomaly Detection
Implement AI-driven anomaly detection algorithms to identify unusual patterns in equipment performance. Tools like AWS SageMaker or Azure Machine Learning can facilitate this process.
3. Predictive Insights Generation
3.1 Predictive Maintenance Scheduling
Generate predictive maintenance schedules based on insights derived from AI analysis, prioritizing equipment based on risk of failure and operational impact.
3.2 Reporting
Create detailed reports and dashboards using tools like Tableau or Power BI to visualize predictive maintenance insights for stakeholders.
4. Maintenance Execution
4.1 Notification System
Set up automated alerts for maintenance teams when predictive maintenance is due. AI-driven tools like Slack or Microsoft Teams can be integrated for real-time notifications.
4.2 Resource Allocation
Utilize AI for optimized resource allocation, ensuring the right personnel and tools are available for maintenance tasks. Tools like ServiceTitan can assist in scheduling and resource management.
5. Continuous Improvement
5.1 Feedback Loop
Establish a feedback mechanism to continuously gather data post-maintenance to refine AI models and improve predictive accuracy.
5.2 Performance Review
Conduct regular performance reviews of the predictive maintenance program, assessing the effectiveness of AI tools and processes implemented.
6. Technology Integration
6.1 Integration with Supply Chain Systems
Ensure seamless integration of predictive maintenance insights with existing logistics and supply chain management systems using APIs or middleware solutions.
6.2 Scalability Planning
Plan for scalability of AI-driven predictive maintenance solutions to accommodate future equipment additions and increased data volumes.
Keyword: Predictive maintenance for logistics equipment