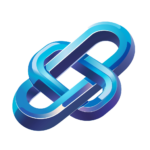
AI Integrated Predictive Maintenance Scheduler Workflow Guide
AI-driven predictive maintenance scheduler enhances operational efficiency by utilizing real-time data analysis and machine learning for timely maintenance interventions
Category: AI Website Tools
Industry: Transportation and Logistics
Predictive Maintenance Scheduler
1. Data Collection
1.1 Sensor Data Acquisition
Utilize IoT sensors installed on vehicles and equipment to collect real-time data on performance metrics such as temperature, vibration, and operational hours.
1.2 Historical Data Analysis
Gather historical maintenance records and operational data to identify patterns and trends that can inform predictive analytics.
2. Data Processing
2.1 Data Cleaning
Implement data preprocessing techniques to eliminate noise and ensure accuracy in the collected data.
2.2 Feature Engineering
Extract relevant features from the raw data that can enhance the predictive models, such as average load, frequency of use, and environmental conditions.
3. Predictive Modeling
3.1 Selecting AI Algorithms
Choose appropriate machine learning algorithms, such as Random Forest, Support Vector Machines, or Neural Networks, to develop predictive models.
3.2 Model Training
Train the selected models using historical data to predict potential failures and maintenance needs.
3.3 Model Validation
Validate the models using a separate dataset to assess their accuracy and reliability in predicting maintenance requirements.
4. Implementation of AI Tools
4.1 AI-Driven Predictive Maintenance Platforms
Utilize platforms like IBM Maximo, GE Predix, or Siemens MindSphere that integrate AI capabilities for predictive maintenance scheduling.
4.2 Real-Time Monitoring Tools
Deploy tools such as Microsoft Azure IoT or AWS IoT Core to facilitate real-time monitoring and data analysis.
5. Maintenance Scheduling
5.1 Automated Alerts and Notifications
Set up automated alerts for maintenance teams based on predictive analytics outcomes, ensuring timely interventions.
5.2 Resource Allocation
Utilize AI algorithms to optimize resource allocation for maintenance tasks, considering factors such as technician availability and parts inventory.
6. Continuous Improvement
6.1 Feedback Loop
Establish a feedback mechanism to continually refine predictive models based on new data and outcomes from maintenance actions.
6.2 Performance Metrics Evaluation
Regularly assess the performance of the predictive maintenance system using key performance indicators (KPIs) such as downtime reduction and maintenance cost savings.
Keyword: Predictive maintenance scheduling tools