Top 5 AI Predictive Maintenance Tools Transforming Manufacturing 2025
Topic: AI Analytics Tools
Industry: Manufacturing
Discover the top 5 AI-powered predictive maintenance tools transforming manufacturing in 2025 for enhanced efficiency reduced costs and minimized downtime
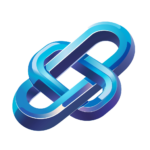
Top 5 AI-Powered Predictive Maintenance Tools Revolutionizing Manufacturing in 2025
Understanding Predictive Maintenance
Predictive maintenance is an advanced strategy that leverages data analytics to predict when equipment failures might occur, allowing manufacturers to perform maintenance at just the right time. This proactive approach minimizes downtime, reduces maintenance costs, and enhances operational efficiency. As we move into 2025, artificial intelligence (AI) is playing a pivotal role in transforming predictive maintenance, making it more accurate and efficient than ever before.
1. IBM Maximo
IBM Maximo is a comprehensive asset management tool that integrates AI to optimize maintenance schedules. With its predictive analytics capabilities, Maximo analyzes historical data and real-time sensor inputs to forecast equipment failures. Manufacturers can utilize this tool to reduce unplanned downtime and extend the lifespan of their assets. The AI-driven insights provided by Maximo help organizations make informed decisions regarding maintenance activities, ensuring that resources are allocated effectively.
2. Siemens MindSphere
Siemens MindSphere is an IoT operating system that harnesses the power of AI to deliver predictive maintenance solutions. By connecting machines and devices, MindSphere collects vast amounts of data that can be analyzed to identify patterns and predict failures. The platform’s machine learning algorithms continuously improve their predictions, allowing manufacturers to stay ahead of potential issues. MindSphere not only enhances maintenance strategies but also drives innovation in product development and operational processes.
3. GE Digital’s Predix
GE Digital’s Predix platform is specifically designed for industrial applications, providing powerful predictive maintenance tools. With its advanced analytics capabilities, Predix can process data from various sources, including sensors and historical maintenance records. The platform uses AI to identify anomalies and predict when maintenance should be performed. This proactive approach helps manufacturers minimize disruptions and optimize maintenance schedules, ultimately leading to increased productivity.
4. PTC ThingWorx
PTC ThingWorx is an IoT platform that enables manufacturers to implement predictive maintenance through AI-driven analytics. ThingWorx collects data from connected devices and applies machine learning algorithms to predict equipment failures. The platform’s user-friendly interface allows for easy integration with existing systems, making it accessible for manufacturers of all sizes. By utilizing ThingWorx, organizations can enhance their maintenance strategies and improve overall operational efficiency.
5. SAP Predictive Maintenance and Service
SAP’s Predictive Maintenance and Service solution is designed to help manufacturers optimize their maintenance processes using AI. The tool analyzes data from various sources, including IoT devices and enterprise systems, to provide actionable insights into equipment health. By predicting potential failures, SAP enables organizations to schedule maintenance activities more effectively and reduce operational disruptions. The integration with SAP’s broader suite of enterprise applications further enhances its utility in manufacturing environments.
Implementing AI in Predictive Maintenance
To successfully implement AI-powered predictive maintenance tools, manufacturers should consider the following steps:
1. Data Collection
Invest in IoT sensors and devices to collect real-time data from equipment. This data forms the foundation for predictive analytics.
2. Integration
Ensure that the chosen predictive maintenance tool integrates seamlessly with existing systems and processes to facilitate data sharing and analysis.
3. Training and Support
Provide training for staff on how to use AI-driven tools effectively. Ongoing support is crucial for maximizing the benefits of predictive maintenance.
4. Continuous Improvement
Regularly review and refine predictive maintenance strategies based on the insights gained from AI analytics. This iterative process will enhance accuracy and effectiveness over time.
Conclusion
As we look ahead to 2025, the integration of AI into predictive maintenance tools is set to revolutionize the manufacturing sector. By leveraging advanced analytics and machine learning, manufacturers can enhance their operational efficiency, reduce costs, and minimize downtime. The tools mentioned above represent just a fraction of the innovations available, but they exemplify the potential that AI holds for the future of manufacturing. Embracing these technologies will be essential for organizations aiming to maintain a competitive edge in an increasingly complex market.
Keyword: AI predictive maintenance tools