Top AI Predictive Maintenance Tools Transforming Manufacturing 2025
Topic: AI App Tools
Industry: Manufacturing
Discover the top 5 AI-powered predictive maintenance tools transforming manufacturing in 2025 and enhancing efficiency while reducing downtime
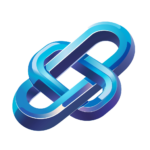
Top 5 AI-Powered Predictive Maintenance Tools Revolutionizing Manufacturing in 2025
As the manufacturing sector continues to evolve, the integration of artificial intelligence (AI) into predictive maintenance strategies is becoming increasingly vital. By leveraging AI, manufacturers can enhance operational efficiency, reduce downtime, and optimize maintenance schedules. In 2025, several AI-powered predictive maintenance tools are set to lead the charge, offering innovative solutions that transform traditional maintenance practices.
1. IBM Maximo
IBM Maximo is an advanced asset management platform that utilizes AI to predict equipment failures before they occur. By analyzing historical data and real-time sensor inputs, Maximo identifies patterns that signal potential issues. This proactive approach allows manufacturers to schedule maintenance activities at optimal times, reducing unexpected breakdowns and extending equipment lifespan.
Key Features:
- Predictive analytics driven by machine learning algorithms.
- Integration with IoT devices for real-time monitoring.
- User-friendly dashboard for tracking asset performance.
2. Siemens MindSphere
Siemens MindSphere is an open IoT operating system that connects industrial machines and systems to the digital world. Its predictive maintenance capabilities harness the power of AI to analyze vast amounts of operational data, enabling manufacturers to gain insights into equipment health and performance trends. This tool not only predicts failures but also recommends actionable steps to mitigate risks.
Implementation:
Manufacturers can implement MindSphere by integrating it with their existing machinery and utilizing its analytics tools to monitor performance metrics. This seamless integration facilitates a shift from reactive to proactive maintenance strategies.
3. GE Digital’s Predix
Predix, developed by GE Digital, is a powerful platform designed specifically for industrial data analytics. It employs AI algorithms to provide predictive insights into asset performance, helping manufacturers avoid costly downtimes. By leveraging machine learning, Predix continuously improves its predictive capabilities, adapting to new data and evolving operational conditions.
Benefits:
- Enhanced decision-making through real-time data analysis.
- Reduction in maintenance costs by prioritizing critical tasks.
- Improved safety through early detection of potential failures.
4. PTC ThingWorx
ThingWorx is a comprehensive IoT platform that empowers manufacturers to create smart, connected solutions. Its predictive maintenance features utilize AI to analyze data from connected devices, offering insights that help optimize maintenance schedules. ThingWorx also provides a robust development environment for creating custom applications tailored to specific manufacturing needs.
Real-World Application:
Manufacturers can deploy ThingWorx to create tailored dashboards that visualize equipment performance and maintenance needs, enabling teams to make informed decisions quickly.
5. Augury
Augury specializes in machine health monitoring through AI-powered diagnostics. By using sensors and advanced analytics, Augury provides real-time insights into the condition of machinery, allowing manufacturers to implement maintenance before failures occur. This tool not only improves operational efficiency but also fosters a culture of proactive maintenance within organizations.
Case Study:
Many manufacturers have reported significant reductions in downtime after implementing Augury, showcasing its effectiveness in real-world applications.
Conclusion
The future of manufacturing is undeniably tied to the advancements in AI-powered predictive maintenance tools. By adopting these innovative solutions, manufacturers can not only enhance their operational efficiency but also foster a culture of continuous improvement. As we move through 2025, the integration of AI into predictive maintenance strategies will be crucial for staying competitive in an increasingly dynamic industry.
Keyword: AI predictive maintenance tools 2025